RFID realizes tobacco warehousing automation and efficient warehouse management
- Share
- Issue Time
- Mar 6,2023
Summary
It is necessary to introduce a new technology to help improve the digital management level of production and logistics in the tobacco industry and achieve a new leap in China's tobacco production, sales, monopoly management, etc. According to the current situation of tobacco enterprises, RFID radio frequency technology is adopted to realize the automation of tobacco warehousing and efficient management of the warehouse.
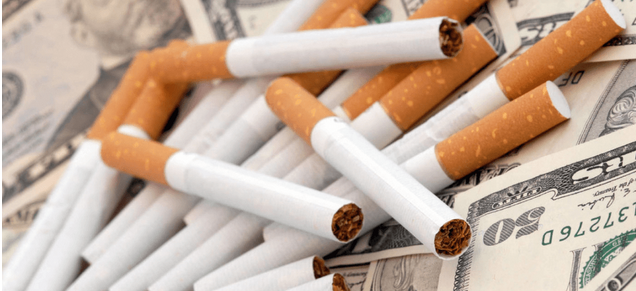
At present, the manual information entry method is still used in many links of tobacco management, and the inventory efficiency of some links is low, and the informatization degree of the whole process is not high. In addition, the anti-counterfeiting technology of tobacco based on barcode also has many problems and limitations.
Therefore, it is necessary to introduce a new technology to help improve the digital management level of production and logistics in the tobacco industry and achieve a new leap in China's tobacco production, sales, monopoly management, etc. According to the current situation of tobacco enterprises, RFID radio frequency technology is adopted to realize the automation of tobacco warehousing and efficient management of the warehouse.
The system takes the middleware as the support platform, attaches RFID tags on cigarette packaging boxes, pallets and shelves, installs RFID access control system at the receiving place, sends the actual receiving and warehousing information to the upper end of the rear end, and the back-end system arranges the warehousing location. At the same time, installs the on-board computer terminal on the forklift, connects the RFID reading and writing equipment, transmits the information between the front-end system and the back-end system through the wireless LAN, and realizes the exchange and update of data, Moreover, the system can locate the forklift in real time, which is convenient for dispatching the forklift.
Semi-automatic method is adopted in the entry and exit operation of elevated warehouse, and certain automation technology and machinery are introduced, supplemented by manual operation, to achieve the balance between efficiency and cost.
The electronic labels are deployed at the bottom of the tray and cigarette stem box, and readers are deployed at the sorting lane, the entry and exit, the exit and the sealing machine correspondingly. In combination with the provisions of the "cigarette production and operation decision management system project in the tobacco industry (i.e., the No. 1 project)", the "one dozen and two sweeps" can be realized. The cigarette industrial enterprises paste the barcode uniformly issued by the competent department on each cigarette produced, and scan the exit code and the entry code of the cigarette commercial enterprises, To enable the tobacco competent department to grasp and implement effective control over the purchase, production and sales information of tobacco enterprises in a timely manner, realize information collection and reasonable connection with the warehouse management system, and transmit data information to the warehouse management system for storage, analysis and processing through the combination of wired and wireless, so as to achieve the goal of rapid and transparent logistics control. In order to carry out effective positioning, first of all, the storage location should be coded, and the coded information should be written into the warehouse management system WMS (usually address coding).
(1) Warehousing business process design / When raw materials and cigarette auxiliary materials are warehoused, use a forklift to put tobacco leaves, tobacco stems, cigarette materials, etc. on the pallets with electronic labels. The reader at the warehouse-in port scans the pallets with electronic labels after the pallets have been coded, completes the matching of pallet information and commodity information, and transmits the matching information to the warehouse management system. Then the conveyor will send the goods to the lane stacker, and the stacker will carry out the warehousing operation.
When finished cigarettes are put into storage, they must be sorted by category through the sorting channel. RFID readers and writers are installed at each sorting crossing. When the cigarettes pass, the RFID electronic labels on the cigarette box are scanned to quickly identify their types. If they meet the types, the side pushing device will push the cigarettes into the channel, and then ABB robots will stack them. After the stacking is completed, the conveyor will send the whole tray of cigarettes to the warehouse entrance, and the RFID readers will scan and record the tray, and then the conveyor will send it to the stacker platform for warehousing.
The warehouse management system (WMS) determines the storage location of this kind of goods and transmits the allocated storage location information to the warehouse control system (WCS) according to the pre-set storage strategy (such as classified random storage), the location assignment principle (such as first in, first out), and the inventory status of goods. The warehouse control system drives the conveyor and lane stacker to complete the warehousing operation.
(2) Issue business process designWhen there are outbound requirements, WMS determines the location of goods to be outbound according to the inventory status and outbound rules, and transmits outbound information (such as the name, quantity, storage location, etc. of outbound goods) to WCS. The warehouse control system WCS drives the lane stacker to take out the goods and send them to the outbound platform through the conveyor. The RFID reader automatically scans the goods or pallet labels for confirmation, completes the update of the cargo location information, and sends the goods to the designated location by shuttle truck, forklift or AGV trolley after there is no error. The outbound operation is completed.
After
the delivery, the pallets will be manually or automatically sent to the
palletizing machine. The WMS will allocate the empty storage space to
the empty tray group, and transmit the information to the warehouse
control system WCS. The warehouse control system WCS will drive the
conveyor and the stacker to send the empty tray group back to the
designated location of the warehouse, and it will be automatically
delivered for use next time.
With the continuous improvement of the automation level of cigarette production, enterprises in the tobacco industry continue to improve production efficiency and ensure product quality by establishing a modern logistics management system. As an extremely efficient, fast and convenient identification technology, RFID technology has been widely used in various industries. Cigarette factories introduce RFID technology into the tobacco industry logistics system, mainly to improve the efficiency of their tobacco industry production and reduce production costs