RFID in the food industry applications
- Share
- Issue Time
- Dec 22,2017
RFID in the food industry applications
Application background
Santa Claus made of chocolate, Easter bunny filled with nougat, or police-style chocolate candy - many of these delicious sweets come from Regensdorf in Rhineland-Palatinate, Germany. Winkler und Dünnebier Süß warenmaschinen GmbH (WDS) supplies processing machinery for the confectionery industry in this small town near Neuve. At the same time, the company is also devoted to developing new pouring / precipitation processes and optimizing existing technologies.
Over the years, the growing international demand for the confectionery industry has ensured the prestige of WDS machinery in the global industry. The company has a wide range of product lines including hard and toffee pouring lines, sandwich and solid chocolate shell casting systems, large starch gating plants, flat chocolate equipment, and universal piston presses for syrup casting. In addition, the company also provides laboratory-use soft candy pouring machines for product research and development in the confectionery industry to meet a wider range of market needs.
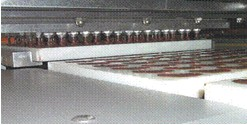
RFID in the food industry applications
The second step in the casting line provides typical fillings, such as creamy almonds or soft syrups. The same principle: heating, filling, cooling. The smooth bottom of chocolate candy - or "lid", which can be said to be chocolate - is made by melting and removing excess syrup and cooling it. At the end of the line, gently tap the back of the mold with an air hammer to peel the candy out of the mold. Conveyor to the finished product into the packaging production line, the mold was left in the chocolate production cycle. They are sent to the mold transfer station to remove debris and become a brand new empty mold spare. The whole system is controlled by PLC and servo motor. PC control terminal or customer service terminal connected with the central server is distributed throughout each pouring machine.
WDS decided to introduce this innovative Near Field Communication (NFC) technology into its confectionery product line, considering the process and order of many manufacturing industries optimized and managed by contactless RFID transponders (tags).
RFID in the food industry applications
To accomplish this project, thousands of plastic pallets in the production floor were fitted with RFID tags. The read-write head on the production line, as well as the remote data acquisition system in the warehouse and production area, are permanently installed so that each mold can be effectively tracked by the central control station during system operation. A database-oriented RFID system ensures the best tracking of molds and products in the production process, in addition to optimizing processes and helping with production data analysis.
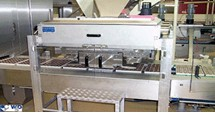
RFID experts in Mülheim, Germany, integrated Turck's read-write heads into the fieldbus system via BL ident I / O modules, enabling WDS's control system to view the latest data at any time for real-time monitoring. Heads are mounted on mold transfer stations and pouring / settling machines and are optionally mounted in weighing and other control sections.
All data collected by the control system is transferred to the factory server's local database, which stores the real-time data of all molds throughout the production cycle. Information generated by the server synchronization for the overall management of the mold and tracking. A complete RFID system includes not only read points on production equipment but also heads in the head and storage system at the mold cleaning station. In accordance with the wishes of customers, WDS allows third parties to transform their legacy systems with Turck RFID products.
High value-added data
Today, Turck's RFID systems ensure that each WDS device's central server database holds valuable information that they can use to optimize plant production and product quality. Data pools may have a wide range of applications, including optimizing logistics. With a single mouse click, the system can display the instantaneous position of any mold, or it's running track across the entire assembly line. As a result, potential sources of error can be easily locked.
RFID in the food industry applications
Production-specific data can also be determined. For example, the system can detect a single mold or even the entire mold group residue content exceeded, and then automatically pick it out. Another application is to compare the die set and the production characteristics of a particular lot.
Data pools also make a difference in quality monitoring and hygiene oversight within the factory, especially in quality management. The system can easily identify whether the current production process is clean. At present, the system can closely track production processes, such as pushing molds together in a freezer or replacing molds with special test molds during system operation, all thanks to RFID technology. If the implanted mold is not suitable for the production process that is currently running, an alert will be given immediately. "Swift" product turnover is also possible under these technical conditions: When the old mold is picked out, the new mold is implanted into the system. Even if the die set is randomly mixed production options are possible, thus increasing the flexibility of production.
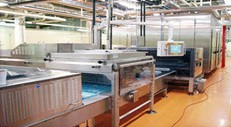